KI.FABRIK BAYERN: Die skalierbare flexible Manufaktur
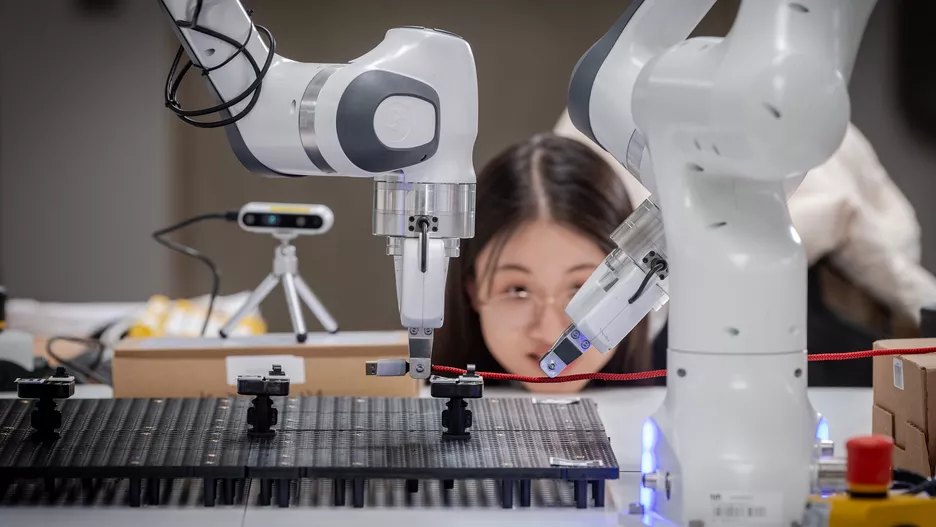
Individuell, flexibel und innovativ: Die Produkte, die sich in Zukunft verkaufen werden, lassen sich nicht mehr auf Basis bestehender Fabrikkonzepte fertigen. In dem Leuchtturmprojekt KI.FABRIK am MIRMI der Technischen Universität München (TUM) geht es deshalb unter anderem darum, Produktionshallen in skalierbare und flexible Manufakturen umzubauen.
„Flexibilität erhöhen“ lautet das Motto des Leuchtturmprojektes KI.FABRIK. Aktuelle Fabriken kommen aus Zeiten der großen Stückzahlen und der Programmierung, in denen der Roboter eine spezielle Aufgabe perfekt und beliebig oft ausführen kann. Für die vielen immer kleinteiliger werdenden Anforderungen durch verschiedene Kunden ist es jedoch nicht mehr möglich, diese Programmierarbeit auch weiterhin zu leisten. Deshalb wird sich die Fabrik wandeln. „Um spezialisierte, individuelle und häufig mechatronische Produkte zu vertretbaren Kosten konstruieren und schnell herstellen zu können, ist eine skalierbare flexible Manufaktur nötig“, ist Prof. Klaus Bengler von der Technischen Universität München (TUM) überzeugt. Diese Fabrik der Zukunft zu schaffen ist das Kernziel des Forschungsprojektes KI.FABRIK.
KI.FABRIK: Die Produktion der Zukunft mit digitalem Zwilling, Roboterarm und Softwareplattform
Selbstlernende Roboter, digitale Zwillinge der Produkte und künstliche Intelligenz spielen Schlüsselrollen in dem bis 2030 laufenden Hightech-Projekt. Die technologische Basis bietet neben dem digitalen Datenabbild der Produktion der Roboterarm „Panda“ des Technologieunternehmens Franka Emika sowie eine entsprechende Softwareplattform. Die Auswahl der Technik und Plattform begrenzen also noch die Einsatzgebiete des Roboters. Doch bietet das nach Ansicht von KI.FABRIK-Projektleiter Prof. Bengler die Möglichkeit zukünftige Lösungen exemplarisch darzustellen. So sieht das „Skill-Konzept“ vor, dass die Fähigkeiten des Roboters auf andere Systeme übertragbar, also plattformunabhängig sind. Der Roboter ist etwa heute schon fähig, über weiter Strecken mit Experten via Teleoperation zu kommunizieren, dessen Arm ist sogar in der Lage, zu fühlen. Zudem weicht er Kollisionen aus und lernt selbst. Ausgestattet mit einem Schlüssel am Greifer findet der Roboterarm selbständig den richtigen Winkel und die richtige Position, um den Schlüssel in den Schlitz zu stecken. Sämtliche Fähigkeiten stehen über eine Softwareplattform (Cloud) auch anderen Robotern zur Verfügung. Dieser Skill lässt sich auf vergleichbare Aufgaben in der Getriebemontage übertragen. „Der Roboter trainiert selbständig und transferiert sein Wissen“, so Prof. Bengler.
Der Weg zur Produktion als digitalem Service
Die Forschungsaufgaben (2021-2025) sind in vier Teilprojekte unterteilt:
- KI.Roboter: In der KI.FABRIK 1.0 wird ein Roboter zur Verfügung stehen, der zunächst von Menschen geführt in die Lage versetzt wird, einzelne Aufgaben zu erlernen. Ziel ist, sich dabei in die Arbeitswelt des Menschen einzufinden und ihnen später beispielsweise monotone oder körperlich anstrengende Aufgaben abzunehmen. Die neu gelernten Fähigkeiten sollen anderen Robotern verfügbar gemacht werden.
- Central AI: Eine zentrale künstliche Intelligenz ist im Umfeld einer skalierbaren und flexiblen Manufaktur entscheidend. Denn hier wird die Fertigung überwacht und ständig optimiert, und zwar über die gesamte Lieferkette hinweg von der Bestellung über die Produktion bis zum Vertrieb. Ziel ist es, möglichst viele Produktionsstufen unter einem Dach ausführen und planen zu können.
- KI.Portal: Über das Softwareportal können Roboter überwacht und kontrolliert werden. Zudem stehen hier die einzeln gelernten Fähigkeiten („Skills“) der Roboter zur Verfügung.
- Production as a Service (PaaS): Die automatische Fertigung individueller Produkte in Losgröße 1 steht am Ende der Entwicklung. Die Vision für 2030: Die Produktion ist als Service zu bestellen wie heute etwa eine App auf dem Handy, per Klick.
Industrielle Unterstützung durch BMW, Wittenstein, Franka Emika, Reactive Robotics und TQ-Systems
Von industrieller Seite unterstützen Autohersteller BMW, der Spezialist für Antriebstechnik Wittenstein sowie das Robotikunternehmen Reactive Robotics die technischen Entwicklungen. Die TUM ist durch Principal Investigators der TUM School of Engineering and Design und der TUM School of Computation, Information and Technology im Konsortium vertreten. Insgesamt steht für das Gesamtprojekt für den Zeitraum von 2021 bis 2025 etwa 13 Millionen Euro zur Verfügung, die primär in den Aufbau von Infrastruktur investiert wird.
Projektleitung
KI.FABRIK BAYERN Forschung und Entwicklung (FuE)
Prof. Achim Lilienthal
Leiter des Lehrstuhls für Perception for Intelligent Systems, TUM School of Computation, Information and Technology, und Principal Investigator am Munich Institute of Robotics and Machine Intelligence (MIRMI), Technische Universität München (TUM).
KI.FABRIK BAYERN Infrastrukture
Prof. Sami Haddadin
Executive Director Munich Institute of Robotics and Machine Intelligence (MIRMI) und Leiter des Lehrstuhls für Robotik und Systemintelligenz, Technische Universität München (TUM).