KI.FABRIK BAYERN: The scalable flexible manufactory
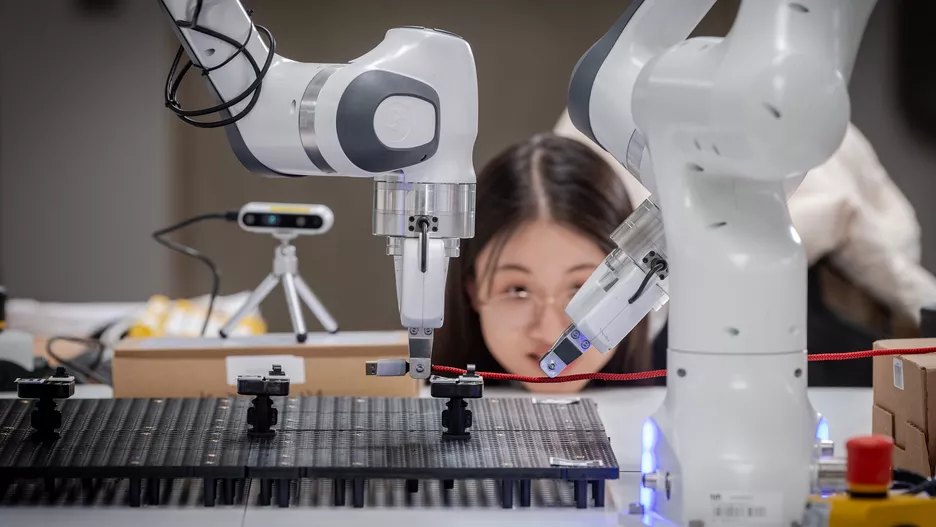
Individual, flexible and innovative: The products that will sell in the future can no longer be manufactured based on existing factory concepts. The lighthouse project KI.FABRIK at MIRMI at the Technical University of Munich (TUM) therefore focuses, among other things, on converting production halls into scalable and flexible manufactories.
"Increase flexibility" is the motto of the lighthouse project KI.FABRIK. Current factories come from times of high volume and programming, in which the robot can perform a specific task perfectly and as often as desired. However, it is no longer possible to continue to do this programming work for the many increasingly small-scale requirements from different customers. That is why the factory will change. “In order to be able to design and quickly manufacture specialized, individual and often mechatronic products at reasonable costs, a scalable flexible manufactory is necessary”, Prof. Klaus Bengler from the Technical University of Munich (TUM) is convinced. Creating this factory of the future is the core objective of the KI.FABRIK lighthouse initiative.
KI.FABRIK: The production of the future with a digital twin, robot arm and software platform
Self-learning robots, digital twins of products and artificial intelligence play key roles in the high-tech project, which will run until 2030. In addition to the digital data image of the production, the technological basis is provided by the robotic arm "Panda" from the technology company Franka Emika and a corresponding software platform. The choice of technology and platform therefore still limit the robot's areas of application. However, according to KI.FABRIK project leader Prof. Bengler, this offers the opportunity to present future solutions as examples. Thus, the "skill concept" provides that the robot's abilities are transferable to other systems, i.e. platform-independent. The robot is already capable of communicating with experts over long distances via teleoperation, and its arm is even able to feel. It also avoids collisions and learns by itself. Equipped with a key on the gripper, the robot arm independently finds the right angle and position to insert the key into the slot. All capabilities are also available to other robots via a software platform (cloud). This skill can be transferred to comparable tasks in gearbox assembly. "The robot trains independently and transfers its knowledge," says Prof. Bengler.
The path to production as a digital service
The first phase (2021-2025) of the research tasks is divided into four sub-projects
- AI.Robot: In the AI.Factory 1.0, humans will initially guide robots to teach them individual tasks. The aim is to integrate into people's working environment in the process and later relieve them of monotonous or physically demanding tasks, for example. The newly learned skills are to be made available to other robots.
- Central.AI: A central artificial intelligence is crucial in the environment of a scalable and flexible manufactory. Because here, production is monitored and constantly optimized throughout the entire supply chain, from ordering to production to distribution. The aim is to be able to carry out and plan as many production stages as possible under one roof.
- AI.Portal: Humans will monitor and control robots via a software portal. In addition, the individually learned abilities ("skills") of the robots are available there.
- Production-as-a-Service (PaaS): The automatic production of individual products in batch size 1 is at the end of the development. The vision: Production can be ordered as a service, like an app on your mobile phone today, with a click.
Industrial support from BMW, Wittenstein, Franka Emika, Reactive Robotics and TQ-Systems
From the industrial side, car manufacturer BMW, drive technology specialist Wittenstein and robotics companies Franka Emika, Reactive Robotics and TQ-Systems are supporting the technical developments. Consortiums integrated by Principal Investigators from the TUM School of Engineering and Design and the TUM School of Computation, Information and Technology represent TUM. In total, about 13 million euros are available for the main projects for the period from 2021 to 2025, which will primarily be invested in the construction of infrastructure.
Project Leadership
KI.FABRIK BAYERN Research and Development (R&D)
Prof. Achim Lilienthal
Head of the Chair “Perception for Intelligent Systems”, TUM School of Computation, Information and Technology, and Principal Investigator at Munich Institute of Robotics and Machine Intelligence (MIRMI), Technical University of Munich (TUM).
KI.FABRIK BAYERN Infrastructure
Prof. Sami Haddadin
Executive Director Munich Institute of Robotics and Machine Intelligence (MIRMI) and Head of the chair of Robotics and Systems Intelligence, Technical University Munich (TUM)