Robotics in production: AI plans flexibly
NEWS, Robotics |
What did you find out?
The developed mobile robot increases value creation in intralogistics. Process times, such as transport, can now be utilized for other tasks. Components can now be placed in designated boxes during transit. Our AI-based task planning decides on the necessary next steps in the production process and continuously adapts to the current system state. It responds continuously to current errors and calculates alternatives to achieve the given goal, such as a fully assembled box, despite a present error. The integrated two-arm solution on the mobile platform allows handling objects of various sizes and properties. Short planning times in the range of seconds enable planning the movements of the robot arms immediately before execution online. The control of the two robot arms reduces the risk of them interfering with each other during cooperative movements, such as jointly gripping an object (e.g., a large box). Additionally, the control of the robot arms compensates for disturbance forces arising from the dynamic movements of the mobile platform.
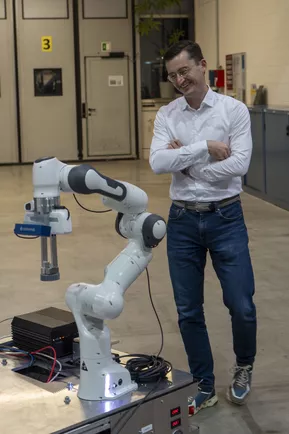
What challenges arose during the research?
Processes in intralogistics must be highly flexible. Therefore, a system had to be developed that continuously adapts to the current system state and any error conditions, such as missing components for assembly or objects to be gripped being at unknown or imprecise locations. It was crucial to reduce planning times. The AI-based task planning approach is highly flexible and requires minimal computation time. Efficient modeling of the environment and improved motion planning algorithms allow for rapidly calculating intuitive movements of the robot arms. Furthermore, handling tasks during transit generate dynamic forces due to the movement of the mobile platform, affecting the accuracy of the robot arms and requiring appropriate countermeasures.
What practical applications does the research have?
The developed control of the two robot arms quickly calculates robot movements that are intuitive for nearby workers. It avoids collisions between the two robot arms under all circumstances while ensuring continuous and fast movement. The software can also be applied to applications with only one robot arm or with a larger number of robots. Therefore, it can be applied to any other production and logistics processes beyond those investigated in the project.
Further Information:
- Video
- Article: Mobile Preassembly Systems with Cooperative Dual-Arm Manipulation - A Concept for Industrial Applications in the Near Future; Jonas Wittmann, Mathias Laile, Johannes Rainer, Johannes Fottner, Daniel Rixen; ISR Robotics 2023; 12-2023.
The results of the research project will be presented to the member companies of bayme vbm on April 18th and 25th, 2024 at 1:00 PM via Teams.
If you are interested, you can register directly at the following link: https://www.baymevbm.de/baymevbm/ServiceCenter/Forschung-Entwicklung/Forschungsprojekte/F-E-Leiter-innen-Nord.jsp
If you do not have direct access, you are also welcome to contact the Managing Director of Kompetenzzentrum Mittelstand GmbH, Dr. Georg Liedl, at georg.liedl(at)kme-mittelstand.de